How Commercial Spray Foam Supports Large-Scale Buildings
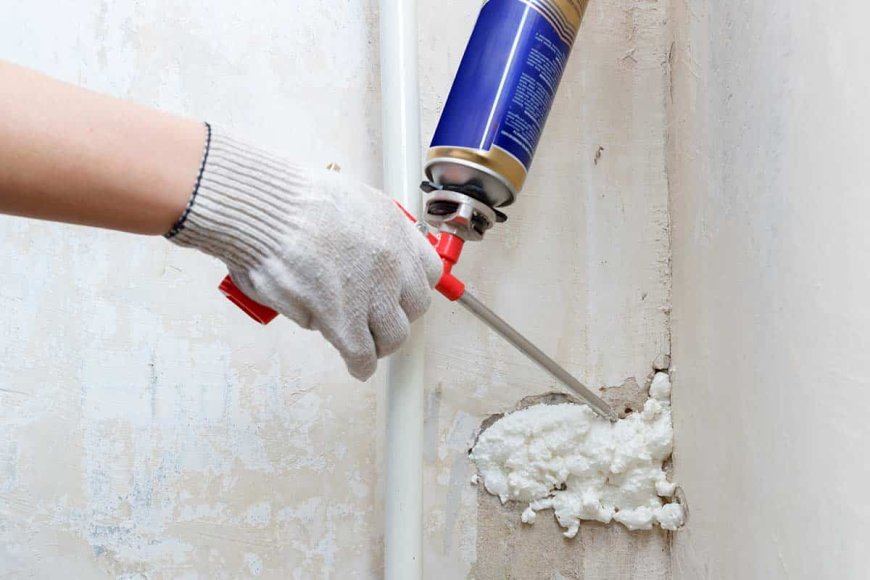
Commercial spray foam insulation plays a vital role in improving the performance and durability of large-scale buildings. From warehouses and manufacturing plants to office complexes and schools, the material offers a combination of air sealing, moisture resistance, and thermal stability that traditional insulation methods often fall short of delivering.
This article explains how commercial spray foam supports large-scale buildings, exploring the structural, environmental, and operational benefits it offers. Readers will gain insights into specific applications, performance expectations, and why it's become a preferred solution for modern commercial construction and retrofits.
Building Envelope Control and Efficiency
Spray foam helps create a consistent, high-performing building envelope, essential for managing energy, moisture, and indoor air quality in large structures.
Air Sealing Capabilities for Massive Structures
Controlling air infiltration in large buildings is challenging due to the scale and number of mechanical penetrations. Spray foam expands on contact, filling irregular gaps and minimizing thermal bypass. It reduces outside air exchange through wall systems and rooflines while improving HVAC efficiency by minimizing conditioned air loss. Occupant comfort also improves through better humidity and temperature stability.
Thermal Performance Across Diverse Climates
Spray foam insulation offers stable R-values and minimizes thermal bridging across walls, roofs, and other envelope areas. Closed-cell foam provides R-6 to R-7 per inch, which helps reduce wall thickness requirements for thermal compliance. It supports LEED and energy code benchmarks and performs well in spaces with high internal heat generation such as production floors or server rooms.
Moisture Resistance and Durability
Moisture is a leading cause of structural degradation in commercial properties. Spray foam insulation helps manage this threat by resisting vapor movement and providing a water-resistant barrier.
Closed-Cell Spray Foam for Moisture Control
Closed-cell foam creates a dense, semi-impermeable barrier that resists water penetration and supports building longevity. It prevents mold and mildew growth in high-humidity environments and reduces reliance on separate vapor barriers in wall and roofing systems. It's especially suited to foundations, below-grade walls, and metal buildings that experience condensation risks.
Long-Term Structural Benefits
Beyond its insulating value, commercial spray foam can improve structural performance. It adds shear strength to wall assemblies, especially in buildings with metal panel systems. When applied to roof decking, it helps resist uplift during wind events. Spray foam maintains its shape and performance over decades without sagging, settling, or absorbing water.
Versatility in Commercial Applications
Spray foam insulation adapts to a wide range of commercial building types and system needs, whether applied during new construction or retrofits.
Common Application Areas in Commercial Buildings
Spray foam is often used on roof decks, particularly flat or low-slope roofs where leaks and ponding water are common. Exterior walls benefit from reduced thermal bridging and improved airtightness. Interior demising walls in offices, schools, and hospitals can gain acoustic and thermal advantages. Mechanical rooms and ductwork coated with spray foam experience fewer condensation problems and better temperature regulation.
Building Area |
Preferred Foam Type |
Key Advantages |
Comments |
---|---|---|---|
Roof Decks |
Closed Cell |
Moisture protection + insulation |
Suited for flat and metal roofs |
Exterior Walls |
Closed Cell |
Air barrier + thermal resistance |
Can be used behind sheathing |
Mechanical Rooms |
Closed Cell |
Controls condensation |
Maintains consistent performance |
Interior Partitions |
Open Cell |
Acoustic absorption |
Useful in sound-sensitive areas |
Energy Savings and Operational Impact
Energy costs in commercial buildings can account for a large portion of annual budgets. Spray foam helps reduce these operating expenses through improved envelope performance.
Reducing HVAC Load and Energy Demand
Spray foam minimizes air infiltration, which directly reduces heating and cooling demands. The consistent insulation layer helps eliminate hot and cold zones. As a result, HVAC systems can be designed at lower capacities, using less energy while maintaining indoor comfort.
Supporting Sustainable Building Certifications
Spray foam contributes to various sustainability goals. Its thermal efficiency helps projects qualify for energy optimization credits under LEED. Many formulations are low in VOCs, improving indoor air quality for WELL and other wellness certifications. Over the long term, spray foam reduces resource consumption by maintaining performance without the need for replacements.
Code Compliance and Safety Considerations
Commercial installations must meet local and national building codes, especially regarding fire performance, occupancy classification, and safety standards.
Fire-Rated and Code-Compliant Installations
Closed-cell foam products must meet fire safety standards such as NFPA 286 and ASTM E84. Depending on the assembly, thermal or ignition barriers may be required. Some products include intumescent coatings or integrated barriers to meet code without additional steps. Installers should follow local jurisdiction requirements and manufacturer guidelines closely.
Integration with Other Building Systems
Spray foam must be installed in coordination with mechanical, plumbing, and electrical systems to avoid overfilling or sealing off service cavities. Installers must ensure substrates are clean, dry, and compatible with foam chemistry. Vapor control strategies should be integrated during design to avoid condensation traps or inconsistent performance.
Common Questions
Is commercial spray foam suitable for metal buildings?
Yes. Closed-cell spray foam adheres to metal surfaces and helps reduce interior condensation. It's commonly used in warehouses, aircraft hangars, and agricultural structures.
How does spray foam handle flat roof applications?
Closed-cell spray foam works well on flat roofs, forming a seamless barrier that prevents water intrusion. It’s typically used under a UV-resistant coating or integrated into an SPF roofing system for added durability.
Can spray foam help with acoustic performance in large buildings?
Open-cell spray foam offers sound absorption and helps reduce airborne noise in shared wall assemblies. It’s often used in educational buildings, offices, and auditoriums to manage acoustics.
How long does commercial spray foam insulation last?
Properly installed spray foam can last over 30 years without needing maintenance. It retains its thermal and air-sealing performance over time.
Conclusion
Expert Spray foam insulation provides lasting value for commercial structures. Its ability to combine air sealing, moisture resistance, and thermal performance makes it well-suited for demanding environments found in large buildings. From energy savings to long-term durability, it offers a measurable improvement over conventional methods.
Its versatility, code compliance potential, and compatibility with modern construction make it a practical choice for professionals managing commercial projects of all sizes.
FAQs
What R-value is recommended for commercial spray foam in walls? Closed-cell spray foam delivers R-6 to R-7 per inch. For most commercial wall assemblies, an R-value between 20 and 30 is typical, depending on climate zone and energy code requirements.
Is spray foam insulation water-resistant or waterproof? Closed-cell foam is water-resistant but not waterproof. It blocks moisture infiltration under normal conditions but shouldn’t be relied on as a substitute for drainage or waterproofing systems.
Can spray foam be applied over old insulation in commercial buildings? Old insulation should be removed if it's wet, damaged, or contaminated. Spray foam requires a clean, stable surface to ensure proper adhesion and long-term performance.
Does commercial spray foam require maintenance? Spray foam does not settle or degrade under normal conditions and requires little to no maintenance. Routine building inspections should include foam-covered areas for any signs of wear or damage.
Are there building code restrictions for using spray foam in commercial spaces? Yes. Building codes may require the use of ignition or thermal barriers, especially in occupied spaces. Compliance depends on application type, location, and local regulations.
Reviewer: Maria Lopez reviewed the article and brought 12 years of insulation industry experience to improve the guidance. Practical tips were added, and the content was made clearer and more useful for contractors working in the field every day