How Commercial Spray Foam Insulation Improves Energy Control
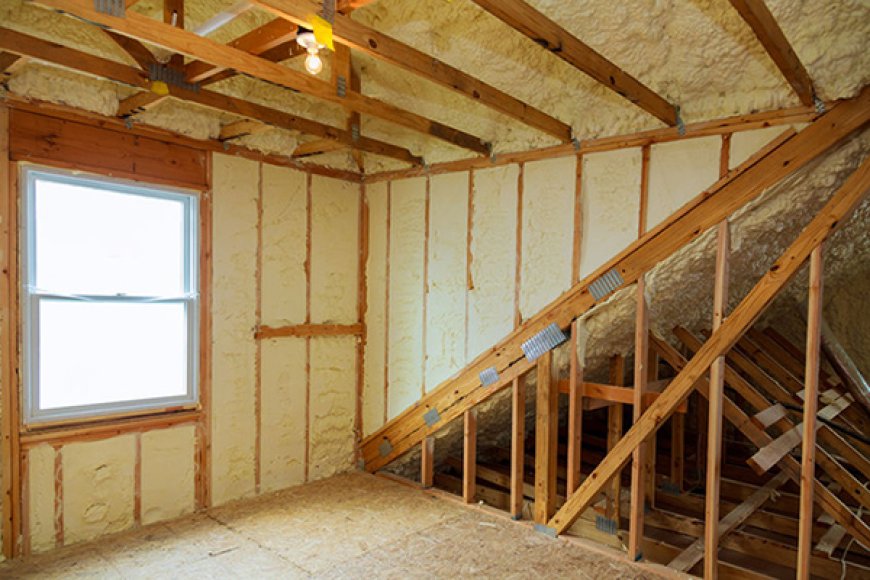
Managing energy consumption in commercial properties can be challenging, especially in buildings with aging infrastructure or inefficient insulation. A significant portion of energy loss in these spaces comes from poor thermal control due to air leaks, insufficient insulation, or inadequate sealing. These issues often lead to escalating HVAC costs and inconsistent indoor temperatures across large facilities.
Spray foam insulation addresses these problems with a combination of thermal resistance and air sealing in one material. Its application in commercial buildings results in better control over energy use, lower operational costs, and improved occupant comfort. This article explores how commercial spray foam insulation supports energy management goals and long-term building performance.
Reducing HVAC Load in Large-Scale Buildings
Commercial properties rely heavily on heating and cooling systems, especially in climates with extreme seasonal temperatures. Improving the insulation envelope significantly eases HVAC demand.
Air Sealing and Load Reduction
Spray foam expands to fill gaps around ductwork, joints, walls, and rooflines—creating an air-tight envelope. This reduces the rate of conditioned air loss, minimizing the cycling of HVAC systems. Fewer cycles mean reduced mechanical strain and less electricity usage across the year.
Consistent Temperature Zones
In large buildings like warehouses or office complexes, uneven temperature zones are common. Spray foam helps maintain consistent thermal conditions across floors and rooms, leading to better environmental control. This is especially helpful in temperature-sensitive environments such as medical facilities, data centers, and food storage areas.
Applications Across Building Components
Commercial structures often include varied building materials and configurations. Spray foam offers a versatile solution that adapts to many areas of a facility.
Roof Decks and Ceiling Cavities
Flat commercial roofs tend to experience significant solar gain and heat loss. Applying closed-cell spray foam to the underside of a roof deck creates a high-performance thermal barrier. It’s particularly effective in low-slope roofs where water and heat penetration are common issues.
Walls and Structural Cavities
Older or poorly insulated wall assemblies leak both air and thermal energy. Spray foam adheres to metal, wood, or masonry and fills voids with minimal loss of space. This allows insulation upgrades in retrofit applications without disrupting structural integrity.
Mechanical Rooms and Utility Chases
Mechanical spaces often contain ductwork and equipment with thermal sensitivity. Spray foam insulates these areas while also helping with sound attenuation and vapor resistance, keeping machinery within optimal operating temperatures and improving energy efficiency.
Cost Savings Through Efficiency
Lowering utility costs is one of the strongest incentives for adopting spray foam in commercial construction or renovation.
Lower Monthly Energy Bills
Spray foam’s high R-value—typically R-6 to R-7 per inch for closed-cell foam—means less energy is required to heat or cool large interior spaces. Property managers often see noticeable drops in utility bills within the first 12 months following insulation upgrades.
Fewer Maintenance Interventions
Efficient insulation reduces wear and tear on HVAC equipment. This translates to fewer service calls, delayed system replacements, and extended lifespans for mechanical systems—providing long-term cost control.
Incentives and Tax Benefits
Many states and utility providers offer energy rebates or deductions for improving commercial building performance. Spray foam qualifies under several programs for energy-efficient upgrades, particularly in LEED-certified and ENERGY STAR-rated projects.
Moisture and Vapor Control in Varied Climates
Controlling moisture is a vital part of energy management in commercial buildings, especially those in humid or wet environments.
Vapor Barrier Functionality
Closed-cell spray foam acts as both insulation and a vapor barrier. This dual purpose prevents condensation from forming inside wall assemblies and roofing systems. Preventing moisture intrusion supports energy efficiency by reducing latent heat loads.
Protection in High-Humidity Zones
Regions with high humidity often experience thermal bridging or mold issues. Spray foam resists water absorption and does not support mold growth, making it suitable for food production spaces, industrial kitchens, and laboratories.
Comparison of Commercial Insulation Methods
Spray foam outperforms traditional materials in nearly every energy-control metric, particularly where both insulation and sealing are needed in one step.
Planning and Execution Considerations
Proper planning ensures that spray foam delivers maximum energy control without unintended consequences.
Retrofit Feasibility
Commercial buildings constructed decades ago often lack cavity space for thick insulation. Spray foam’s high R-value per inch makes it suitable for tight retrofit conditions. Installers can inject foam into existing cavities through small access points, reducing disruption to building operations.
Fire Ratings and Code Compliance
All commercial insulation products must meet fire and building code standards. Spray foam must be covered with a thermal or ignition barrier in most commercial applications. Professional installers evaluate code requirements and apply protective coatings where needed to maintain safety and compliance.
Common Questions
Can spray foam be used in high-rise commercial buildings?
Yes. Spray foam is used in high-rise buildings for wall insulation, HVAC zones, and roof assemblies. Its air-sealing properties help stabilize temperatures across multiple floors.
Does spray foam qualify for green building certifications?
Yes. Spray foam contributes to energy efficiency credits under programs like LEED and ENERGY STAR. Using low-GWP (global warming potential) products may also improve sustainability scores.
Is it safe to install sensitive electronic equipment?
Once cured, spray foam is inert and safe around servers and electronics. Installation should occur when areas are unoccupied, and proper ventilation must be maintained during curing.
What maintenance does spray foam insulation require?
Spray foam requires little to no maintenance after installation. Occasional visual inspections in accessible areas can confirm that the insulation remains intact and undamaged.
Conclusion
Spray foam insulation offers a measurable return on investment for commercial buildings seeking better energy control. It reduces energy waste by sealing air leaks, maintaining consistent internal temperatures, and preventing moisture intrusion. Whether applied during construction or retrofitted into older spaces, spray foam strengthens a building’s ability to manage heating and cooling demands effectively.
For property owners and facility managers focused on long-term savings, expert spray foam provides reliable performance and supports better HVAC efficiency with minimal disruption. With correct installation and attention to code compliance, it remains a trusted tool for commercial energy optimization.
FAQs
How long does commercial spray foam insulation last? Properly installed spray foam can last 50 years or more. It does not sag, compress, or degrade like other forms of insulation, maintaining energy performance for decades.
Can spray foam reduce HVAC equipment size needs? Yes. Because it reduces air loss and thermal transfer, HVAC systems can often be downsized or operate more efficiently, leading to lower equipment and operating costs.
Is spray foam suitable for metal buildings? Spray foam adheres well to metal and prevents condensation on steel surfaces. It’s widely used in commercial warehouses and pre-engineered metal buildings.
Does spray foam insulation improve sound control? Open-cell spray foam can reduce airborne sound transmission, making it beneficial in commercial offices or mixed-use spaces needing acoustic control.
What’s the best season to install commercial spray foam? Installation is possible year-round but generally more efficient in mild weather. Extreme heat or cold can affect curing times and may require adjustments in application technique.
Reviewer: Olivia Thompson has spent 10 years working in spray foam insulation, helping companies grow their visibility. She reviewed this article and provided valuable suggestions on how to better align the content with the needs and expectations of customers, ensuring it resonates with the target audience.